As travel restrictions are slowly eased and airlines start to offer more regular connections, airports are looking for ways how to implement improved hygiene standards and social distancing guidance throughout the passenger journey without compromising security, efficiency or profitability. Achieving this is likely to be a key factor in gaining a competitive advantage in the recovery phase.
The security checkpoint presents unique challenges due to the typically high contact nature of the screening process and the tendency for bottlenecks at this point in the passenger journey. Parallel divest stations have been introduced to help reduce one bottleneck by improving tray throughput. In response to COVID-19, social distancing measures have seen some of these divest stations closed to create space between passengers as they divest their belongings at the checkpoint. In turn, this will likely create reductions in throughput.
In their recovery recommendations, “Take-off: Guidance for Air Travel through the COVID-19 Public Health Crisis”, the International Civil Aviation Organization recently proposed the:
“Rearranging of security checkpoint access and layouts should be considered with the objective of reducing queues and crowding to the extent possible while maintaining desirable throughput. This should include both divestment areas and those areas where passengers retrieve their screened cabin baggage.”
There are several interdependencies at the checkpoint that when working together create flow, or when they do not work together, can create bottlenecks and reduce throughput. These include the physical checkpoint components (divest stations, baggage scanners, people screening, reclaim and recheck areas); processes and workflows; and the staff and passengers at the checkpoint. In order to avoid any bottlenecks and achieve the best outcome, it is important to understand these interdependencies and look at the checkpoint as a whole, as well as its individual elements.
Used for years to help design security checkpoints, Smiths Detection’s advanced checkpoint simulation tool does exactly that, and is now being used to predict the impact of social distancing at checkpoints. To illustrate how our simulation tool can help we’ve looked at a lane style, that should be familiar to many airports.
Checkpoint Scenario
In this scenario, we compare a standard 20 metre long lane with five available divest stations – (as would have been common before the covid-19 pandemic) – with the same lane but only three divest stations available to allow for distance to be maintained between passengers. We also looked at the influence that the number of analysts and recheck operators deployed in the screening area can have on the reduction of tray throughput. Though there are, of course, many other factors to consider, for simplicity we have reduced the number of variables to these two factors to show their interdependency.
Using our simulation tool we were able to show that a reduction of up to 25 percent in tray throughput per hour could be expected when only three out of five divest stations are being used.
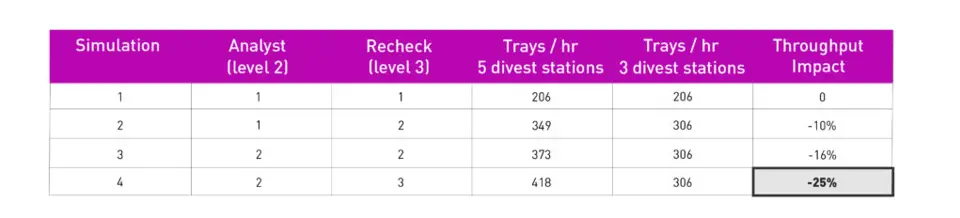
It is however worth noting that the impact on throughput grows when more image and recheck analysts have been deployed.
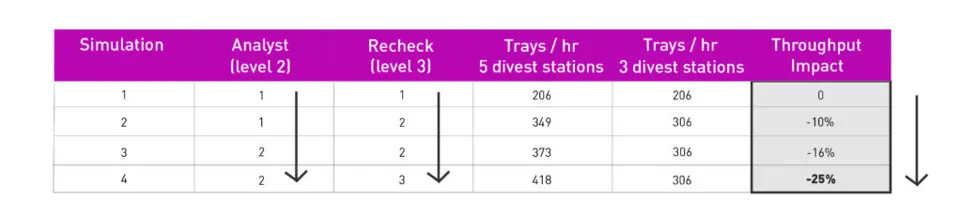
Simulation 1, for example, produced the same number of trays/hr with three stations as with five. This is due to the combination of having only one analyst and one recheck operator deployed, which can create bottlenecks at the X-ray image screening and tray recheck. The lane is therefore not capable of processing more than 206 trays, no matter how many divest stations are being used.
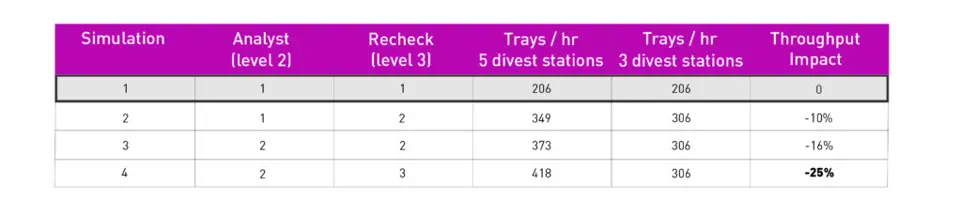
The throughput of the lane can be more than doubled from 206 to up to 418 trays/hr by deploying additional operators at recheck and image analysis when five divest stations are open. With only three divest stations open, you can also significantly improve tray throughput by adding an additional operator to recheck (206 to 306 trays/hour).
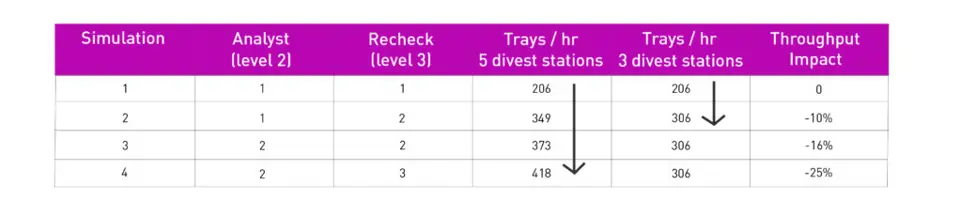
The throughput will however stagnate at 306 trays/hour even if you deploy more operators. The reason for this is that in our scenario each passenger was given an average of 35 seconds to divest items into a tray. This means that there is a maximum potential of 102 trays that passengers can divest per hour per divest station. Divestment is therefore the bottleneck in simulations 2, 3 and 4 when only three divest stations are open and adding more staff does not have any positive impact.
As with any checkpoint project, it is very important to get the balance of the different parts right especially when considering the implementation of social distancing measures. We are very happy to partner with you for a complete review of your operations, predict the impact of such measures and identify improvement opportunities by adapting technology, processes and staff deployment. While the changes caused by the COVID-19 pandemic are likely to stay with us for some time, it is also advisable to plan for a time beyond the crisis and how throughput levels can be adapted to cater for the gradually rising passenger numbers we look forward to seeing again soon.